Teilen:
ADDITIVE MANUFACTURING LAB VERGRÖSSERT
Das Additive Manufacturing Lab des Lehrstuhls für Kunststoffverarbeitung (KV) hat seinen Maschinenpark um einen freeformer 200-3X der Firma ARBURG erweitert. Mit diesen Anlagen sowie einem neuen Verfahren geht das Unternehmen neue Wege im Additive Manufacturing.

Eingerichtet wurde der freeformer von Franz Kynast (Manager Additive Manufacturing bei ARBURG). Abgebildet auf dem Foto: v. l. n. r.: Dr. Joamin Gonzalez-Gutierrez (wissenschaftli¬cher Mitarbeiter KV), Frank Kynast (Manager Additive Manufacturing bei ARBURG), Prof. Clemens Holzer (Leiter KV), Dipl.-Ing. Stephan Schuschnigg (Leiter der Arbeitsgruppe Extrusion und Additive Fertigung)
Das AKF-Verfahren (ARBURG Kunststoff-Freiformen) ermöglicht die Verwendung von Granulaten, die in zwei Spritzeinheiten aufgeschmolzen werden und durch Nadelverschlussdüsen tröpfchenweise auf das Bauteil aufgebracht werden.
Das Beste aus zwei Technologien: 3-D-Druck & Spritzguss kombiniert
Durch diese neue Technologie lassen sich Bauteile im industriellen Maßstab herstellen, die je nach Orientierung und Material, mit Festigkeiten ähnlich denen von spritzgegossenen Bauteilen überzeugen können, aber gleichzeitig eine individuelle, optimierte Geometrie aufweisen.
„Das bedeutet, wir können damit die Vorteile von ansonsten zwei sehr unterschiedlichen Verfahren kombinieren: Wir sind – wie im 3-D-Druck – in der Lage individuelle Produkte zu generieren, die je nach Anwendung gezielt angepasst und optimiert werden können. Gleichzeitig gibt es kaum Einschränkungen beim Material, da man mit Granulaten – wie im Spritzguss – arbeitet. Das eröffnet uns viele Möglichkeiten, vor allem in Hinblick auf medizinische Anwendungen. Wir freuen uns schon darauf, mit der Anlage die Erforschung der Additiven Fertigungstechnologien an der Montanuniversität Leoben weiter voranzutreiben“, erläutert Univ.-Prof. Dipl.-Ing. Dr.mont. Clemens Holzer, Leitung Lehrstuhl für Kunststoffverarbeitung
Neue Technologie vor allem für Medizintechnik gewinnbringend
Dieses Verfahren ist insbesondere im Projekt CAMed Clinical additive manufacturing for medical applications (FFG Fördernr. 871132; weitere Informationen auf www.kunststofftechnik.at) von Bedeutung, dessen Ziel es ist, patientenspezifische Implantate herzustellen. Dabei wird auch an Multimaterialkomponenten geforscht: Flexible und starre Materialien sollen dabei miteinander verbunden werden, um eine Beweglichkeit der Implantate zu gewährleisten.
Durch die Möglichkeit, auch Granulate verarbeiten zu können, können viele Kunststoffe verwendet werden, die eine medizinische Zulassung aufweisen und für die Anwendung im klinischen Bereich geeignet sind. Dadurch ergeben sich zahlreiche Materialkombinationen, die für Implantate genützt werden könnten.
Weitere Informationen
Univ.-Prof. Dipl.-Ing. Dr.mont. Clemens Holzer
Lehrstuhl für Kunststoffverarbeitung
E-Mail: clemens.holzer(at)unileoben.ac.at
Tel.: +43 3842 402 – 3500
Dipl.-Ing. Stephan Schuschnigg
Lehrstuhl für Kunststoffverarbeitung
E-Mail: stephan.schuschnigg(at)unileoben.ac.at
Tel.: +43 3842 402 – 3511
Berg- und Hüttenmännische Monatshefte
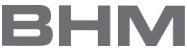
Zeitschrift für Rohstoffe, Geotechnik, Metallurgie, Werkstoffe, Maschinen- und Anlagentechnik
Journal of Mining, Metallurgical, Materials, Geotechnical and Plant Engineering